I. Przegląd procesów kucia
Kucie to proces obróbki metali, który polega na zastosowaniu sił zewnętrznych w celu wywołania odkształcenia plastycznego w materiałach metalowych, uzyskując w ten sposób odkuwki o określonych kształtach, rozmiarach i właściwościach. W zależności od temperatury kucia, kucie można podzielić na kucie na gorąco, kucie na ciepło i kucie na zimno. W oparciu o mechanizm formowania, kucie można podzielić na kucie swobodne, kucie matrycowe, walcowanie pierścieniowe i kucie specjalne. Różne procesy kucia są odpowiednie dla różnych scenariuszy zastosowań i wymagań produktowych.
II. Procesy kucia elementów podwozia maszyn inżynieryjnych (cztery koła i jeden pas)
A. Kucie na gorąco
Kucie na gorąco polega na podgrzewaniu metalowych półfabrykatów do określonej temperatury przed kuciem. Nadaje się do dużych i skomplikowanych kształtów elementów podwozia. Kucie na gorąco może skutecznie poprawić wewnętrzną strukturę metali, zwiększyć plastyczność i wytrzymałość materiału, a tym samym wytwarzać wysokiej jakości odkuwki. W produkcji elementów podwozia maszyn inżynieryjnych kucie na gorąco jest powszechnie stosowane do produkcji kluczowych części, takich jak ogniwa gąsienic, koła pasowe i rolki nośne.
B. Kucie matrycowe
Kucie matrycowe polega na umieszczaniu metalowych półfabrykatów w matrycach o określonych kształtach. Można je podzielić na kucie w matrycach otwartych i kucie w matrycach zamkniętych. Kucie matrycowe może wytwarzać odkuwki o złożonych kształtach i wysokiej dokładności wymiarowej, dzięki czemu nadaje się do produkcji masowej. W przypadku elementów podwozia maszyn inżynieryjnych kucie matrycowe jest często wykorzystywane do produkcji części, takich jak koła napędowe i gąsienice. Kucie w matrycy zamkniętej i spęczanie zamknięte to zaawansowane procesy kucia matrycowego. Ponieważ nie ma wypływek, wykorzystanie materiału jest wysokie i możliwe jest wykonanie precyzyjnej obróbki złożonych odkuwek w jednej lub kilku operacjach. Bez odprysków, powierzchnia styku odkuwki jest zmniejszona, a wymagane obciążenie jest również zmniejszone. Ważne jest jednak, aby upewnić się, że półfabrykat nie jest całkowicie ograniczony. Dlatego konieczne jest ścisłe kontrolowanie objętości półfabrykatu, względnego położenia matrycy kuźniczej i pomiaru odkuwki oraz podejmowanie wysiłków w celu zmniejszenia zużycia matrycy.
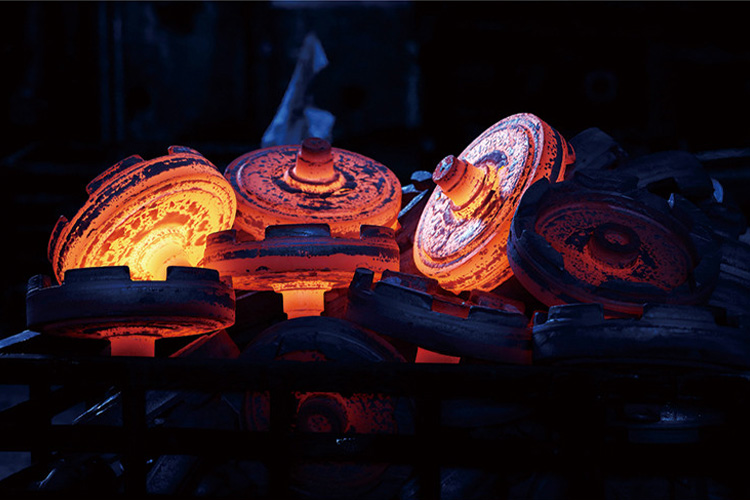
C. Walcowanie pierścieni
Walcowanie pierścieni to proces produkcji części w kształcie pierścieni o różnych średnicach przy użyciu specjalistycznych maszyn do walcowania pierścieni. Jest on również wykorzystywany do produkcji części w kształcie koła, takich jak felgi samochodowe i koła pociągów. W przypadku elementów podwozia maszyn inżynieryjnych, proces walcowania pierścieni może być wykorzystywany do produkcji dużych części w kształcie koła, takich jak koła napinające i rolki nośne. Procesy walcowania pierścieni mogą zapewnić dokładność wymiarową i właściwości mechaniczne części w kształcie pierścienia, spełniając surowe wymagania maszyn inżynieryjnych dla elementów podwozia.
D. Kucie specjalne
Kucie specjalne obejmuje procesy takie jak kucie walcowe, walcowanie poprzeczne klinowe, kucie promieniowe i kucie matrycowe w stanie ciekłym, które są odpowiednie do produkcji części o specjalnych kształtach. Na przykład kucie walcowe może być stosowane jako skuteczny proces wstępnego formowania w celu znacznego zmniejszenia ciśnienia formowania w kolejnych operacjach; walcowanie poprzeczne klinowe może wytwarzać części takie jak stalowe kule i wały napędowe; kucie promieniowe może wytwarzać duże odkuwki, takie jak lufy pistoletów i wały stopniowane. W produkcji elementów podwozi maszyn inżynieryjnych, specjalne procesy kucia mogą spełnić specjalne wymagania różnych części, poprawić wydajność produkcji i jakość produktu.
III. Zalety procesu kucia UCP
A. Zaawansowany sprzęt i technologia
UCP wprowadziło zaawansowany sprzęt do kucia i technologie procesowe z całego świata, aby zapewnić wydajność i stabilność procesu kucia. Dzięki zastosowaniu zaawansowanych pras hydraulicznych, młotów kuźniczych i innych urządzeń, możliwe jest precyzyjne kontrolowanie temperatury, ciśnienia i szybkości odkształcania podczas procesu kucia, uzyskując w ten sposób wysokiej jakości elementy podwozia. Ponadto UCP jest również wyposażone w zaawansowany sprzęt testujący do monitorowania procesu kucia w czasie rzeczywistym, zapewniając, że jakość produktu spełnia normy.
B. Ścisła kontrola jakości
Firma UCP wprowadziła rygorystyczny system zarządzania jakością. Od zakupu surowców po wysyłkę gotowego produktu, każde ogniwo przechodzi ścisłą kontrolę jakości. Podczas procesu kucia UCP zwraca uwagę na kontrolę kluczowych parametrów, takich jak temperatura nagrzewania półfabrykatu, wielkość deformacji kucia i zużycie matrycy, aby zapewnić jakość wewnętrzną i powierzchniową odkuwek. Ponadto UCP regularnie konserwuje i kalibruje sprzęt, aby zapewnić jego normalne działanie, zapewniając w ten sposób stabilność jakości produktu.
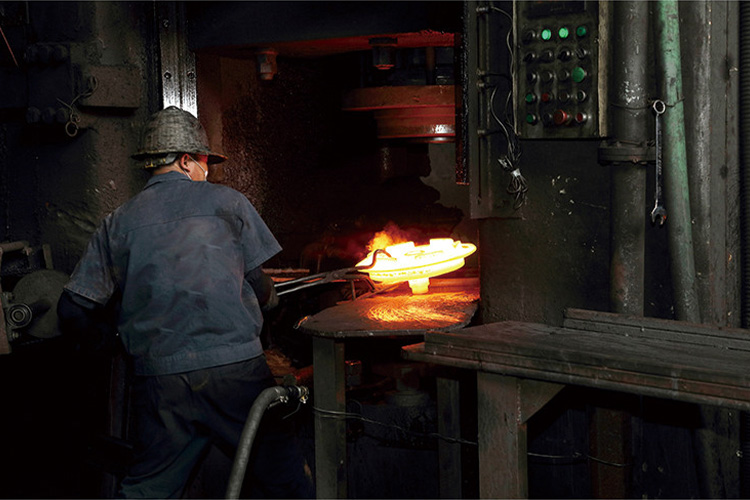
C. Usługi niestandardowe
UCP może zapewnić niestandardowe rozwiązania w zakresie kucia w oparciu o potrzeby klienta. Niezależnie od tego, czy chodzi o kształt, rozmiar czy wymagania dotyczące wydajności produktu, UCP może zapewnić spersonalizowane usługi kucia dzięki profesjonalnemu zespołowi technicznemu i zaawansowanemu sprzętowi. Ta niestandardowa usługa nie tylko spełnia specjalne potrzeby klientów, ale także zwiększa wartość dodaną produktu i zwiększa konkurencyjność firmy na rynku.
IV. Wnioski
Procesy kucia elementów podwozia maszyn inżynieryjnych (cztery koła i jeden pas) są kluczem do zapewnienia jakości i wydajności produktu. Dzięki zaawansowanemu sprzętowi, ścisłej kontroli jakości i usługom dostosowanym do indywidualnych potrzeb, UCP zgromadziło bogate doświadczenie w dziedzinie kucia i może dostarczać klientom wysokiej jakości, wysokowydajne komponenty podwozia. W przyszłości UCP będzie nadal koncentrować się na innowacjach technologicznych i doskonaleniu procesów, stale zwiększając swoje możliwości w zakresie kucia i wnosząc większy wkład w rozwój przemysłu maszyn inżynieryjnych.