I. Overview of Forging Processes
Forging is a metalworking process that involves applying external forces to cause plastic deformation in metal materials, thereby obtaining forgings with specific shapes, sizes, and properties. Depending on the forging temperature, forging can be categorized into hot forging, warm forging, and cold forging. Based on the forming mechanism, forging can be divided into free forging, die forging, ring rolling, and special forging. Different forging processes are suitable for different application scenarios and product requirements.
II. Forging Processes for Engineering Machinery Undercarriage Components (Four Wheels and One Belt)
A. Hot Forging
Hot forging involves heating metal blanks to a certain temperature before forging. It is suitable for large-sized and complex-shaped undercarriage components. Hot forging can effectively improve the internal structure of metals, enhance material ductility and toughness, and thus produce high-quality forgings. In the production of engineering machinery undercarriage components, hot forging is commonly used to manufacture key parts such as track links, idler wheels, and carrier rollers.
B. Die Forging
Die forging involves placing metal blanks into forging dies with specific shapes. It can be divided into open-die forging and closed-die forging. Die forging can produce forgings with complex shapes and high dimensional accuracy, making it suitable for mass production. In engineering machinery undercarriage components, die forging is often used to manufacture parts such as drive wheels and track shoes. Closed-die forging and closed upsetting are advanced processes in die forging. Since there is no flash, material utilization is high, and it is possible to complete the precision machining of complex forgings in one or several operations. Without flash, the contact area of the forging is reduced, and the required load is also decreased. However, it is important to ensure that the blank is not completely restricted. Therefore, it is necessary to strictly control the volume of the blank, the relative position of the forging die, and the measurement of the forging, and to make efforts to reduce die wear.
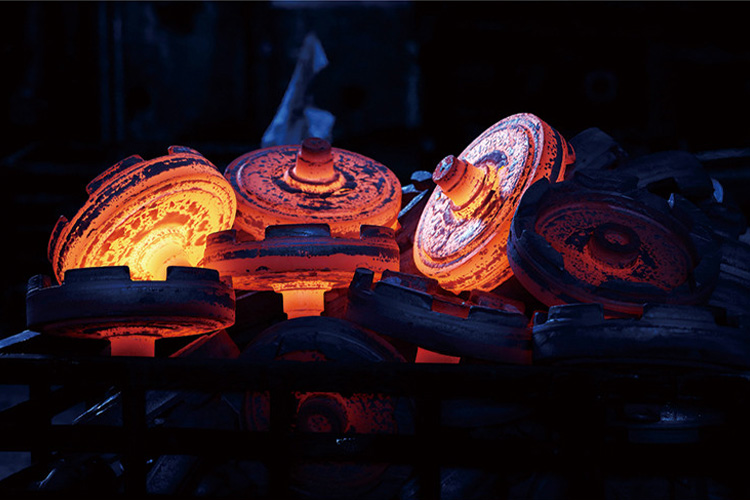
C. Ring Rolling
Ring rolling is the process of producing ring-shaped parts of different diameters using specialized ring rolling machines. It is also used to manufacture wheel-shaped parts such as automotive rims and train wheels. In engineering machinery undercarriage components, the ring rolling process can be used to produce large wheel-shaped parts, such as idler wheels and carrier rollers. Ring rolling processes can ensure the dimensional accuracy and mechanical properties of ring-shaped parts, meeting the strict requirements of engineering machinery for undercarriage components.
D. Special Forging
Special forging includes processes such as roll forging, wedge cross rolling, radial forging, and liquid die forging, which are suitable for producing parts with special shapes. For example, roll forging can be used as an effective preforming process to significantly reduce the forming pressure in subsequent operations; wedge cross rolling can produce parts such as steel balls and drive shafts; radial forging can produce large forgings such as gun barrels and stepped shafts. In the production of engineering machinery undercarriage components, special forging processes can meet the special requirements of different parts, improve production efficiency, and product quality.
III. UCP’s Forging Process Advantages
A. Advanced Equipment and Technology
UCP has introduced advanced forging equipment and process technologies from around the world to ensure the efficiency and stability of the forging process. By using advanced hydraulic presses, forging hammers, and other equipment, it is possible to precisely control the temperature, pressure, and deformation rate during the forging process, thereby obtaining high-quality undercarriage components. In addition, UCP is also equipped with advanced testing equipment to monitor the forging process in real-time, ensuring that product quality meets standards.
B. Strict Quality Control
UCP has established a strict quality management system. From raw material procurement to finished product shipment, every link undergoes strict quality inspection. During the forging process, UCP pays attention to the control of key parameters such as the heating temperature of the blank, the forging deformation amount, and die wear, to ensure the internal and surface quality of the forgings. In addition, UCP regularly maintains and calibrates equipment to ensure its normal operation, thereby ensuring the stability of product quality.
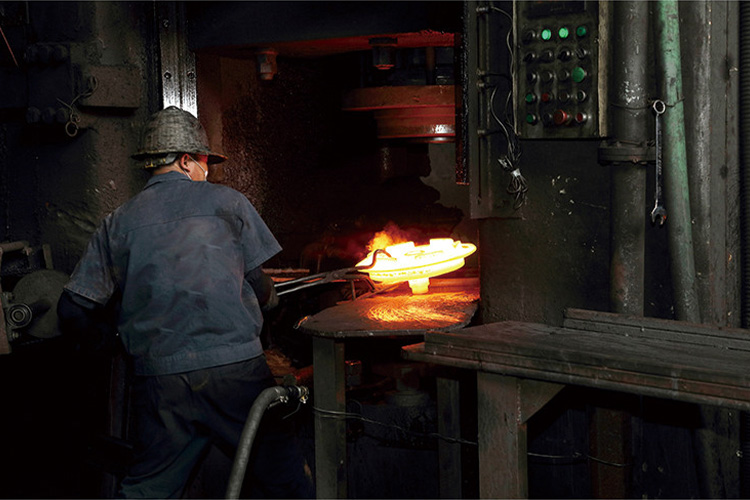
C. Customized Services
UCP can provide customized forging solutions based on customer needs. Whether it is the shape, size, or performance requirements of the product, UCP can provide personalized forging services through its professional technical team and advanced equipment. This customized service not only meets the special needs of customers but also increases the added value of the product and enhances the company’s market competitiveness.
IV. Conclusion
The forging processes for engineering machinery undercarriage components (four wheels and one belt) are key to ensuring product quality and performance. With advanced equipment, strict quality control, and customized services, UCP has accumulated rich experience in the forging field and can provide high-quality, high-performance undercarriage components for customers. In the future, UCP will continue to focus on technological innovation and process improvement, constantly enhancing its forging process capabilities, and making greater contributions to the development of the engineering machinery industry.