I. Hazards in Forging Production
A. Mechanical Injuries
- Mechanical Injuries: Direct injuries caused by machines, tools, or workpieces, such as cuts and bruises.
- Burns: Forging production is conducted in high-temperature environments, and workers are prone to burns from contact with hot metals and equipment.
- Electrical Injuries: Forging equipment typically requires electrical power. Improper use or malfunction of electrical equipment can lead to electrical shock accidents.
B. Environmental Factors
- High-Temperature Radiation: Forging production is carried out with metals in a red-hot state. For example, the forging temperature range for low-carbon steel is between 1250-750℃. The extensive manual labor increases the risk of workers suffering burns.
- Thermal Radiation: Heating furnaces and red-hot ingots, blanks, and forgings continuously emit large amounts of radiant heat. Workers exposed to high-temperature environments for extended periods are susceptible to the effects of thermal radiation.
- Dust and Fumes: During the combustion process, heating furnaces produce dust and fumes that are released into the workshop air. This not only affects hygiene but also reduces visibility within the workshop, increasing the likelihood of work-related accidents.
- Noise and Vibration: Forging equipment generates noise and vibration during operation, creating a noisy and distracting work environment. This can affect workers’ hearing and nervous systems, increasing the risk of accidents.
C. Equipment and Tool Factors
- Equipment Malfunctions: Forging equipment, such as air hammers, steam hammers, and friction presses, operate under impact forces. These machines are prone to sudden failures when subjected to impact loads. For example, the sudden breakage of a forging hammer piston rod can cause severe injuries.
- Tool Management: A wide variety of forging tools and auxiliary tools are used. These tools are often stored haphazardly, and their frequent replacement makes it difficult to inspect them properly. Using inappropriate tools can lead to work-related accidents.
- Improper Operation: Forging equipment exerts significant force. For example, crank presses, stretching forging presses, and hydraulic presses have considerable working forces. If dies are not installed or operated correctly, most of the force may act on the dies, tools, or equipment itself, leading to equipment damage or personal injury.
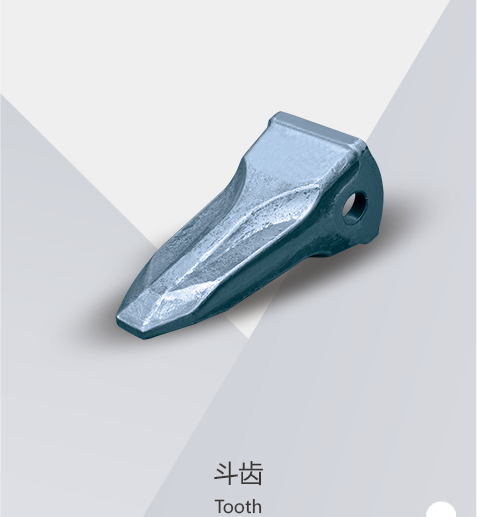
II. Control Methods for Hazards in Forging Production
A. Control of Mechanical Injuries
- Install Protective Devices: Install protective devices and safety equipment in areas and on equipment that require protection to ensure safety during operation. This is particularly important for equipment used in the production of excavator carrier rollers and track carrier rollers.
- Regular Equipment Inspections: Regularly inspect the protective devices on equipment to ensure they are in good condition and functioning properly. This is crucial for maintaining the safety of workers handling carrier rollers and excavator sprockets.
- Equipment Maintenance: Regularly maintain equipment to promptly repair defects or malfunctions, ensuring its normal operation. This is essential for the reliable production of excavator idler assemblies and excavator track chains.
- Operational Training: Provide technical and safety training for operators to ensure they understand the correct operational procedures and methods. This is particularly important for those working with excavator sprockets and excavator idler wheels.
B. Control of Environmental Factors
- Ventilation Systems: Install effective ventilation systems to reduce dust and thermal radiation in the workshop, improving the working environment. This is especially important for workers involved in the production of excavator carrier rollers and excavator sprockets.
- Thermal Insulation Measures: Implement thermal insulation measures around high-temperature equipment to mitigate the effects of thermal radiation on workers. This is crucial for those working with excavator idler assemblies and excavator track chains.
- Noise Control: Use soundproofing materials and equipment to reduce the impact of noise and vibration on workers. This is essential for maintaining a safe and efficient work environment, particularly for those working with excavator sprockets and excavator idler wheels.
- Personal Protective Equipment: Provide workers with personal protective equipment that meets the working conditions, such as safety glasses, work clothes, and work shoes. This is particularly important for those handling excavator carrier rollers and excavator sprockets.
C. Control of Equipment and Tool Factors
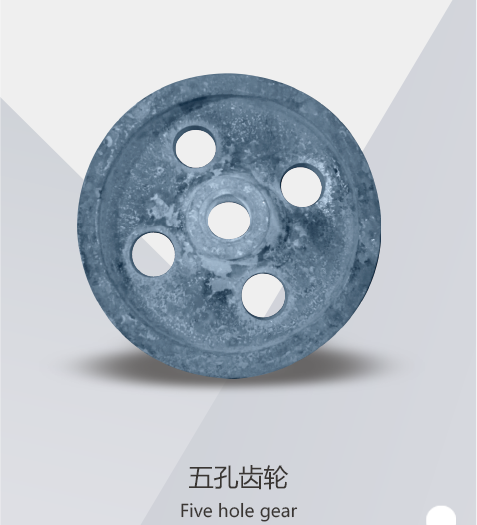
- Tool Management: Organize and manage tools properly to ensure they are stored orderly and easily accessible for quick retrieval and use. This is especially important for tools used in the production of excavator carrier rollers and excavator sprockets.
- Operational Standards: Establish strict operational standards for equipment to ensure correct die installation and operation, preventing accidents caused by improper operation. This is crucial for the production of excavator idler assemblies and excavator track chains.
- Pre-Operational Inspections: Conduct thorough inspections of equipment before operation to ensure all components are in good condition. This is essential for the reliable production of excavator carrier rollers and excavator sprockets.
- Team Coordination: Ensure coordination and cooperation among team members when multiple people are working on a task together to prevent accidents caused by poor coordination. This is particularly important for those working with excavator idler assemblies and excavator track chains.
III. Conclusion
Forging production is of irreplaceable importance in the mechanical manufacturing industry, especially for the production of undercarriage components such as excavator carrier rollers, excavator sprockets, and excavator idler assemblies. These components are essential for the stability and performance of heavy machinery like excavators and bulldozers. However, the hazardous factors in the production process cannot be ignored. By implementing effective control measures, the risk of accidents in forging production can be significantly reduced, thereby improving production efficiency and product quality. UCP is always committed to enhancing production safety and efficiency. Through advanced equipment, strict quality control, and customized services, we provide customers with high-quality, high-performance products. We believe that through continuous technological innovation and process improvement, forging production will become safer, more efficient, and more environmentally friendly.